Coolant ⚙️⚙️⚙️
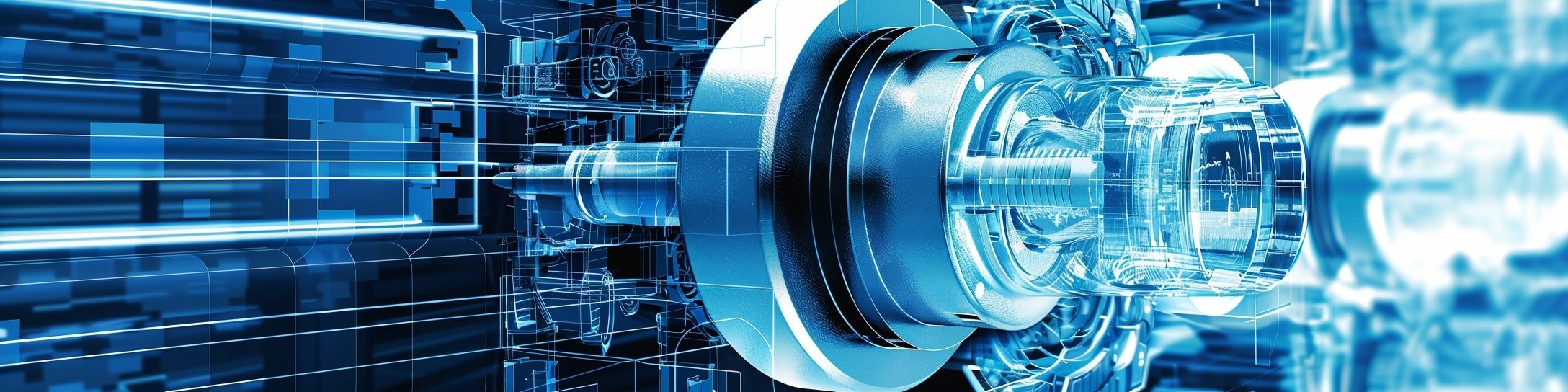
Coolant, also known as cutting fluid, is a crucial fluid used in metalworking and machining processes. Its primary functions include cooling the workpiece and cutting tool, reducing friction and heat, preventing tool overheating, and flushing away metal debris from the cutting process.
Types of Coolants
Straight Oils: These non-emulsifiable oils are used undiluted in machining operations. They offer excellent lubrication and significantly extend tool life.
Soluble Oils: These oils emulsify with water to form a milky solution, providing good cooling and lubrication properties.
Semi-Synthetic Coolants: Combining soluble oils and synthetic components, these coolants offer the advantages of both oil-based and synthetic coolants, providing effective cooling and lubrication.
Synthetic Coolants: These water-based coolants contain no petroleum or mineral oil. They offer excellent cooling capabilities and are generally cleaner than oil-based coolants.
Composition
Coolants can be composed of various substances, including petroleum distillates, animal fats, plant oils, water, and gases. They come in several forms such as oils, oil emulsions, pastes, gels, aerosols (mists), and air or other gases.
Choosing the Right Coolant
Selecting the appropriate coolant depends on several factors:
Machining Operation: Different operations require different cooling and lubrication properties.
Workpiece Material: The material being machined can dictate the type of coolant needed.
Tool Type: Specific tools may benefit more from certain coolant properties.
Environmental Considerations: Coolants should be chosen with regard to their environmental impact and safety.
Benefits
Using the right coolant correctly can significantly extend the life of cutting tools and improve the quality of the finished workpiece. Proper coolant use ensures efficient heat dissipation, reduces wear on tools, and enhances overall machining performance.
In CNC machining, an axis defines a direction of movement, with linear axes (X, Y, Z) for basic motion and rotational axes (A, B, C) for complex, angled machining.
CNC dust extraction systems remove dust and debris from machining, enhancing safety, cleanliness, and air quality in CNC operations, especially with dust-prone materials.
A CNC enclosure is a protective cabinet that houses CNC machines, enhancing safety by containing debris, reducing noise, and controlling the machining environment.
A CNC lathe is a precision machine tool that uses computer programming to control cutting tools, achieving accurate shaping of rotating workpieces for complex geometries.
CNC EDM (Electrical Discharge Machining) utilizes CNC technology to automate precise, non-contact machining, ideal for complex shapes and hard materials.
Learn about CNC milling spindles, their function, design, and importance in precise, repeatable machining. Discover key features and operational insights.
A CNC (Computer Numerical Control) milling machine is a computer-controlled machine tool used to remove material from a workpiece to create custom parts with complex shapes and profiles.
CNC machining is a manufacturing process that uses computer numerical control (CNC) to automate the operation and movement of machine tools, enabling precise and accurate control of machining operations such as milling, turning, drilling, and grinding.
A CNC router is a computer-controlled cutting machine used for cutting, shaping, and engraving various materials, such as wood, plastic, and softer metals.
A CNC (Computer Numerical Control) machine is a computer-controlled manufacturing tool that automates the movement and operation of cutting tools to perform various machining processes, such as milling, turning, drilling, and cutting.
Discover the importance of coolants in CNC machining, including types, benefits, and selection tips. Enhance tool life and machining performance.
Electrical Discharge Machining (EDM) is a precision process that uses electrical discharges to shape hard materials, ideal for intricate contours and cavities in various industries.
A jig is a custom-made tool in CNC machining that holds and guides workpieces, ensuring accuracy, repeatability, and efficiency during production processes.
Live tooling in CNC lathes allows for powered rotary tools, enabling operations like milling, drilling, and tapping, enhancing versatility and precision in a single setup.
A milling spindle is the core component of a milling machine, responsible for rotating the cutting tool at precise speeds, ensuring stability and accuracy during machining operations.
A machining centre is a highly automated CNC machine tool capable of performing multiple operations like milling, drilling, and tapping in a single setup for efficient, precise manufacturing.
Milling is a versatile machining process using rotary cutters to shape materials into precise forms and contours, widely applied in industries like aerospace and automotive.
A spray mist coolant system delivers a fine mist of coolant during machining to cool and lubricate the cutting tool and workpiece, extending tool life and improving surface finish.
Small Hole EDM, or EDM drilling, is a precision process used to create tiny, deep holes in hard, conductive materials, ideal for industries like aerospace and energy.
Sinker EDM, also known as die-sinking EDM, uses a shaped electrode to create precise cavities and complex geometries in conductive materials, ideal for intricate molds and dies.
A vacuum table pump is a vital component in machining, providing the suction needed to securely hold a workpiece on the table, ensuring stability and precision without traditional clamps.
A vacuum table is a specialized work-holding device in machining that uses suction to secure a workpiece, allowing for stable, obstruction-free machining without the need for traditional clamps.
Wire EDM is a high-precision machining process that employs electrical discharges to cut conductive materials, using a thin wire electrode to create intricate shapes without physical contact.
A CNC vacuum table is a work-holding device that uses vacuum pressure to securely hold workpieces in place during machining, ensuring stability and precision.