5.0 Robotics Executive CNC Routers ATC System
Automation - Quality Improvement - Skill Delegation
Allows a skilled operator to set up the machine, configure tooling, apply tool offsets, run test programs, and validate the system.
Once set up, a less skilled operator can oversee production, focusing on monitoring the machine and handling minor interruptions.
Tool Replacement
Broken tools can be replaced by removing the tool holder, reloading a replacement tool, and recalibrating the tool offset.
The process ensures quick recovery and minimal downtime during production.
Cost-Effective Use
Avoids high costs associated with proprietary systems, allowing seamless integration with existing CAD/CAM workflows.
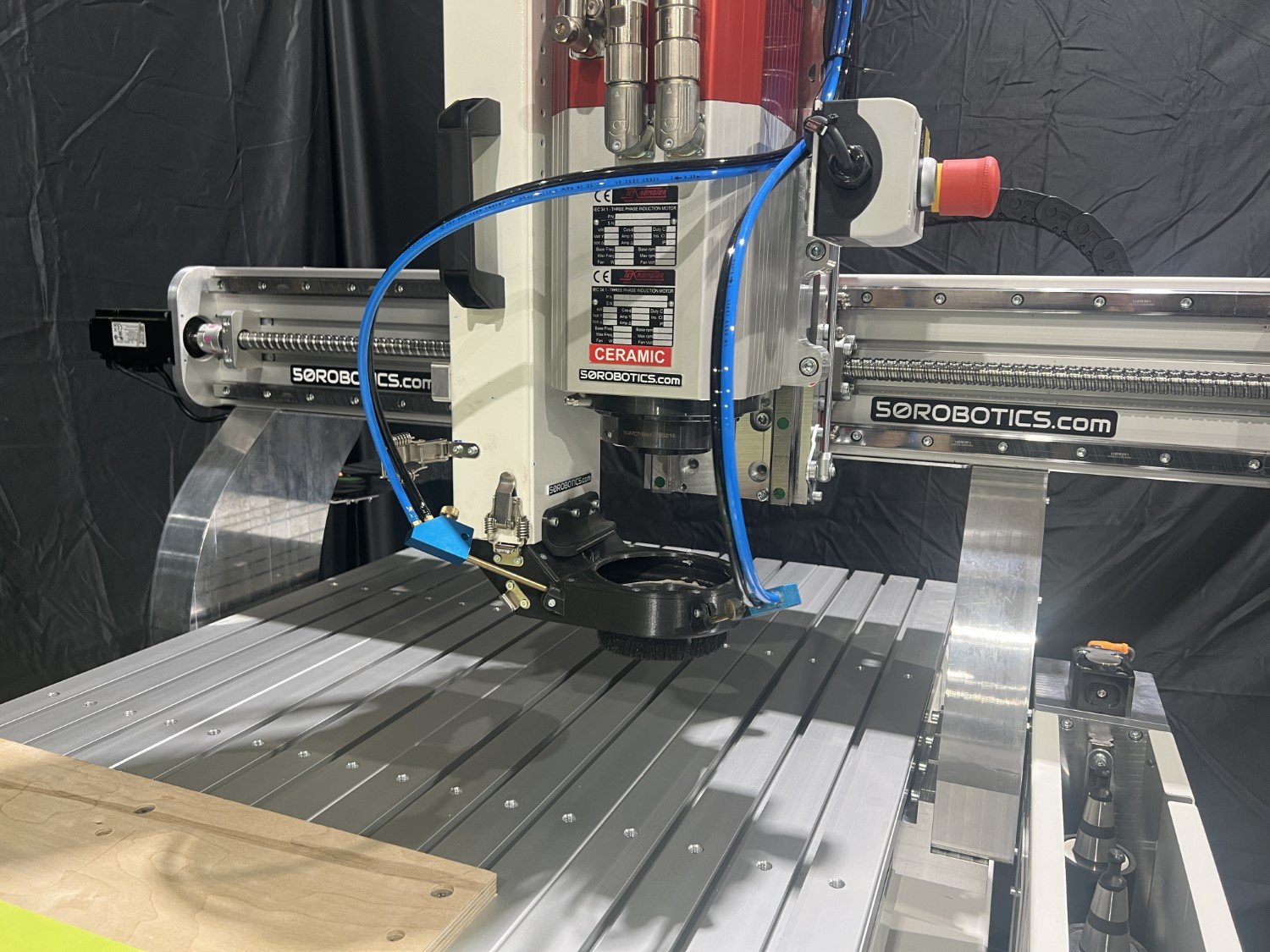
50 Robotics offer all machines with IS30 ATC.
-
50 Robotics now offer all machines with full automated tool changing
-
The system runs a 9 tool ATC magazine where pneumatics rise and lower an ATC magaine. All tools are picked and dropped automatically
-
All ATC systems have an automated touch off tool offset sensor. This allows each tool to automatically have their offsets set.
5.0 ATC supported for all models
ISO30 ATC
9 tool ATC
Automated offset sensor
Dust shoe fully integrated
UCCNC Plug and Play
The Automatic Tool Changer (ATC) system on the EXECUTIVE CNC machines is designed to enhance efficiency and productivity in machining operations. Key features include:
ISO30 ATC Compatibility: The system supports ISO30 tool holders, facilitating quick automated and precise tool changes.
9-Tool Magazine: Equipped with a magazine that holds up to 9 tools, allowing for seamless transitions between different machining tasks without manual intervention.
Single-Phase Power Supply: Operates on a 220V AC domestic supply, making it suitable for various workshop environments without the need for three phase power.
High-Speed Spindle: Features a spindle capable of reaching up to 24,000 RPM, ensuring efficient material removal and high-quality finishes.
Precision and Reliability: Incorporates a piston-driven ATC mechanism and additional sensors to ensure accurate tool changes and enhanced safety during operations.
This ATC system is particularly beneficial for complex machining tasks requiring multiple tools, as it reduces downtime and increases overall productivity. Its integration into the EXECUTIVE CNC machines reflects a commitment to providing advanced, user-friendly solutions for modern manufacturing challenges.
The Executive CNC platform integrates advanced automation systems for spindle operation, tool magazine management, and offset sensing. Complementing these features is the highly engineered floating dust shoe system, designed to work seamlessly with the Automatic Tool Change (ATC) process. This integration ensures a clean, efficient, and user-friendly production environment. Below are the key features and capabilities of the floating dust shoe system:
Floating Dust Shoe System
Height Adjustability: The dust shoe height can be set independently to match the workpiece surface.
Spindle Interaction: The spindle moves in and out of the dust shoe, allowing for continuous operation without manual intervention.
Automatic Retraction: The shoe retracts to a safe height automatically when the spindle moves to its designated safe position. This functionality ensures:
Safe tool changes.
Accurate offset sensing.
Seamless Integration with ATC Process
The dust shoe remains in its production location throughout operations, facilitating stable and hassle-free tool changes.
During tool changes or offset sensing, the shoe retracts without requiring manual adjustment, maintaining its efficiency and precision.
This integration supports full production workflows without interruptions, enhancing the machine’s automated capabilities.
Efficient Chip and Dust Extraction
High-Performance Extraction: When connected to the shoe, the dust extraction system effectively removes chips and debris from the cutting zone, ensuring a clean workspace.
Fog Buster Integration: The system supports dual-nozzle Fog Buster or similar misting systems, which can be integrated directly into the base of the shoe. The features include:
Nozzles directed at the cutting tool for precise air and coolant delivery.
Full compatibility with the dust extraction system, even during tool changes.
Efficient evacuation of debris while maintaining cooling and lubrication at the cutting zone.
Compact and Automated Design
Production Footprint: The system operates within a compact footprint of 2 meters by 1 meter, ideal for various production environments.
Power Requirements: Operates on single-phase power, making it accessible for a wide range of facilities.
Nine-Tool Capacity: Fully automated production across nine tools ensures efficiency and flexibility in machining operations.
User Benefits
Clean, tidy, and efficient machining environment.
Hassle-free operation with minimal manual intervention.
High compatibility with various cutting and misting systems.
Enhanced precision and safety during automated workflows.
This innovative floating dust shoe system, integrated with the Executive CNC platform, delivers unmatched functionality and performance, making it a reliable choice for advanced automated manufacturing.
ATC System Dust Shoe
The floating dust shoe is fully integrated into the ATC system.
Fixed lower location with integration of the misting nozzles maximises the shoes performance.
Seamless integration of extraction system
Auto lift to safe height for full retract for ATC.
Automatic Tool Changer (ATC) Overview for the EXECUTIVE CNC Platform
1. Core Features
ISO30 Tool Holder System:
Utilizes standardized ISO30 tool holders with an ER32 collet system.
Enables preloaded tools with fixed offsets for seamless and efficient tool changes.
9-Tool Magazine:
Allows storage and management of up to nine tools.
Incorporates an automatic offset calibration system, saving tool offsets in a centralized tool table.
2. Mechanism and Sensors
Piston-Driven Tool Change:
Operates via an air piston for gripping and releasing tools.
Controlled by solenoids, enabling software-based automation.
Allows fully automatic loading and unloading of tools.
The spindle can move to a location, drop a current tool, and pick up a new tool with preloaded holders.
Advanced Sensor Integration:
Monitors spindle RPM, piston position, collet state, and tool engagement.
Detects and flags errors like sticky pistons, misaligned tool racks, or low air pressure, ensuring robust fault detection.
3. Offset Management
Tool Offsets:
Each tool in the magazine has an associated offset saved to the tool table.
Offsets allow relative measurement in the Z-axis, compensating for tool length variations.
Tools can be automatically calibrated using a fixed offset sensor located at the back of the machine.
The sensor ensures accurate offsets by measuring the Z-axis travel required to trigger it based on tool length.
Z-Zero Translation:
Workpiece reference (Z-Zero) is automatically adjusted across tool changes.
Eliminates the need for manual recalibration between tools during machining.
4. Remote and Off-Grid Operation
Operates on a 220V domestic single-phase power supply.
Demonstrated use cases include operation:
From the power outlet of a Ford Transit vehicle.
Using a low-cost single-phase diesel generator.
Fully off-grid with connectivity via a 4G/5G tether for remote support and diagnostics.
Remote operations were successfully demonstrated with the machine physically located in Estonia while controlled from Dublin.
5. Dust Shoe System
Automatic Retraction:
Dust shoe automatically lifts to a safe height during tool changes or offset calibration.
Efficient Extraction:
Fully compatible with misting systems like Fog Buster, ensuring optimal cooling and chip evacuation during operations.
6. Ease of Use and Setup
Pre-calibrated at the factory; requires no additional setup on-site.
Includes a configuration file for quick deployment and start-up.
7. Power and Portability
Compact footprint (2m x 1m) and light power requirements make it ideal for mobile applications.
Demonstrated capability to machine parts discreetly inside a vehicle, enhancing portability and versatility.
8. Reliability and Engineering
Built on the proven ATC 71 spindle platform, ensuring durability and field-tested reliability.
Strong and rigid EXECUTIVE CNC frame supports the 20 kg spindle effortlessly.
9. Software and Connectivity
Fully integrated with the UCCNC controller, running on a Windows 10 PC.
Supports remote diagnostics, real-time monitoring, and cloud-based error logging.
Fully compatible with high-end CAD/CAM packages like SolidCAM, Fusion 360, HSM, and HyperMill, using standard ISO G-code without encryption or expensive post-processors.
10. Operator Skill Delegation and Process Efficiency
Skill Delegation:
Allows a skilled operator to set up the machine, configure tooling, apply tool offsets, run test programs, and validate the system.
Once set up, a less skilled operator can oversee production, focusing on monitoring the machine and handling minor interruptions.
Tool Replacement:
Broken tools can be replaced by removing the tool holder, reloading a replacement tool, and recalibrating the tool offset.
The process ensures quick recovery and minimal downtime during production.
Cost-Effective Use:
Avoids high costs associated with proprietary systems, allowing seamless integration with existing CAD/CAM workflows.
11. Additional Notes
The ATC system is now available on all 5.0 Robotics CNC machines. It features an air-piston-driven mechanism for tool gripping and release, controlled via solenoids and software, enabling fully automatic loading and unloading of tools. The spindle uses ISO30 tool holders and an ER32 collet system, supporting a standardized and efficient tool change process. Each tool has a saved offset in the tool table, calibrated using a fixed offset sensor. The system's automation eliminates manual recalibration during tool changes and ensures high accuracy. The ATC system includes a 9-tool magazine and robust fault detection via advanced sensor integration, monitoring spindle RPM, piston position, and tool engagement. It also supports off-grid operation and seamless remote control.